Metal 3D Printing
The revolutionary technology that lets you materialize any complex mechanical component.
Speak to our Additive Manufacturing experts to find out how we can help.
Metal 3D Printing
The revolutionary technology that lets you materialize any complex mechanical component.
Speak to our Additive Manufacturing experts to find out how we can help.
Metal 3D Printing in Brief
Metal 3D Printing in Brief
Metal 3D printing or Metal Additive Manufacturing is a revolutionary technology which produces components directly from 3D CAD data. The 3D CAD data is cut into numerous sections, and these sections are printed one over the other to get the final component.
A major advantage of the technology is to produce parts with complex geometries which are difficult to manufacture through conventional techniques. 3D Printing offers the flexibility to design parts for their functionality rather than designing the parts for their manufacturability.
Metal 3D printing is used to manufacture one off prototypes, small batch production parts, series production parts and die and mould repair. Different Metal AM methods such as Powder Bed Melting, Binder Jetting and Direct Energy Deposition have their own advantages.
At Rapid DMLS, we use the most popular technique of Direct Metal Laser Sintering which yields the best part properties and has the ability to produce complex geometries.
Metal 3D printing or Metal Additive Manufacturing is a revolutionary technology which produces components directly from 3D CAD data. The 3D CAD data is cut into numerous sections, and these sections are printed one over the other to get the final component.
A major advantage of the technology is to produce parts with complex geometries which are difficult to manufacture through conventional techniques. 3D Printing offers the flexibility to design parts for their functionality rather than designing the parts for their manufacturability.
Metal 3D printing is used to manufacture one off prototypes, small batch production parts, series production parts and die and mould repair. Different Metal AM methods such as Powder Bed Melting, Binder Jetting and Direct Energy Deposition have their own advantages.At Rapid DMLS, we use the most popular technique of Direct Metal Laser Sintering which yields the best part properties and has the ability to produce complex geometries.
How DMLS Works
How DMLS Works
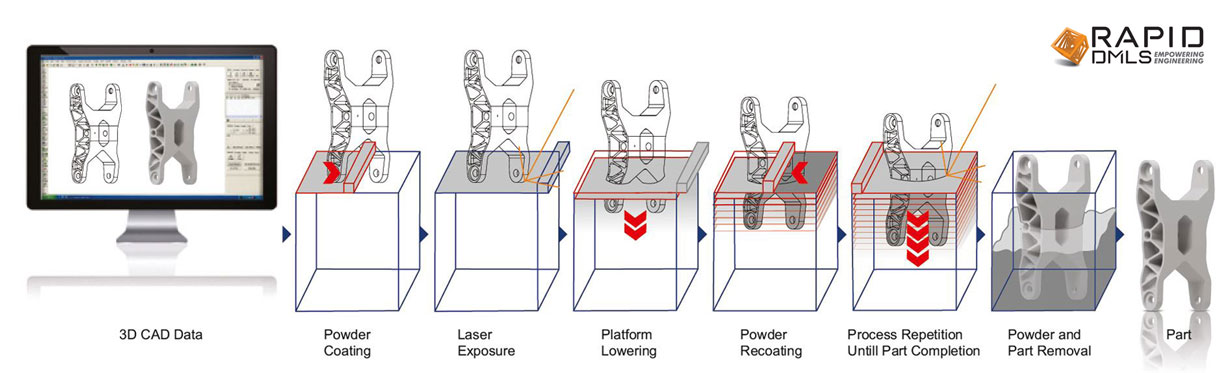
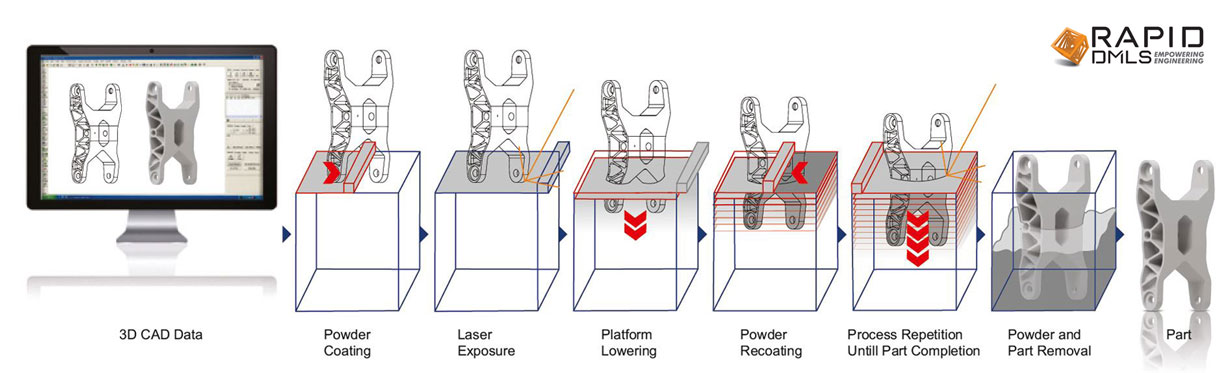
How We Can Help You with DMLS
How We Can Help You with DMLS
Pre Processing
Pre Processing
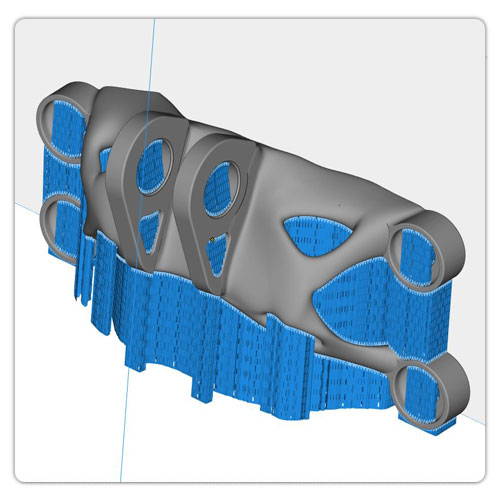
- Part Feasibility: Not every part is suited for Additive Manufacturing. Based on the part quantity, size, complexity and material, we suggest whether going additive is the best option.
- Reverse Engineering: When you want to print a part, but do not have the necessary drawings and details, we can generate the 3D models using CMM machines and Laser Scanning.
- Design for Additive Manufacturing: Not every pre-existing design can be printed right away. We optimise your design to make it print-friendly by reducing the mass while retaining the same strength.
- Data Preparation: Once your 3D Cad data is received, we decide the best printing orientation and assign suitable support structures to ensure a successful build with best part quality.
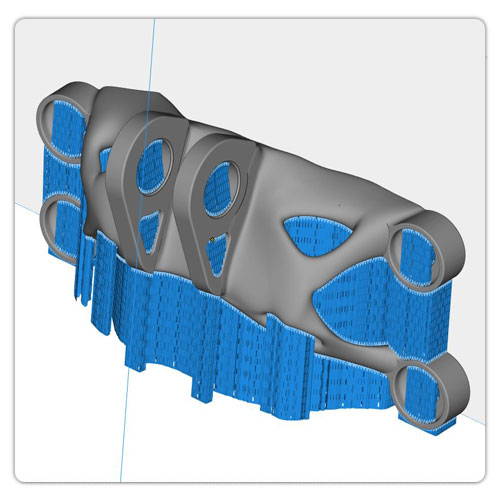
- Part Feasibility: Not every part is suited for Additive Manufacturing. Based on the part quantity, size, complexity and material, we suggest whether going additive is the best option.
- Reverse Engineering: When you want to print a part, but do not have the necessary drawings and details, we can generate the 3D models using CMM machines and Laser Scanning.
- Design for Additive Manufacturing: Not every pre-existing design can be printed right away. We optimise your design to make it print-friendly by reducing the mass while retaining the same strength.
- Data Preparation: Once your 3D Cad data is received, we decide the best printing orientation and assign suitable support structures to ensure a successful build with best part quality.
3D Printing
3D Printing
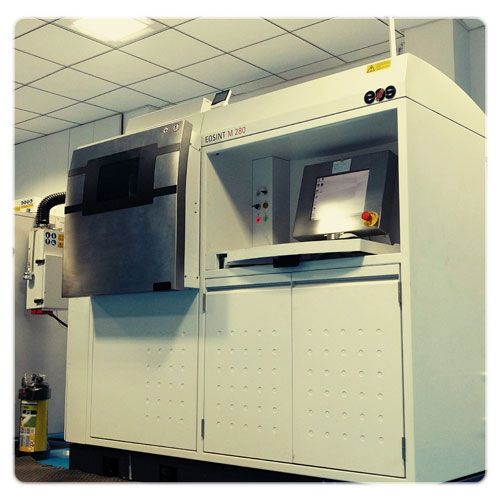
- The analysed CAD data is sliced into numerous layers and the corresponding process parameters are set to get high quality surface finish and part properties.
- We use an EOS M280 Direct Metal Laser Sintering machine with a build envelope of 250mm x 250mm x 300mm equipped with a 400W Laser.
- To prevent oxidation, the build chamber is filled with inert gas and the oxygen content in the chamber is maintained at less than 0.1%.
- The parts are built on a pre-heated metal substrate which keeps going down by a layer thickness after each layer is printed, until the final layer is printed.
- Once printing is done, the part is allowed to cool down for a short period and the parts are unloaded for further post-processing.
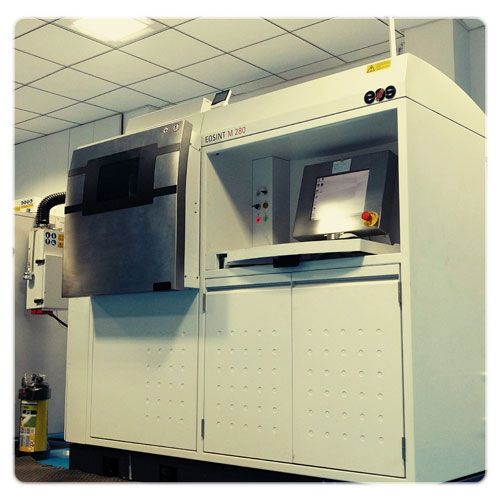
- The analysed CAD data is sliced into numerous layers and the corresponding process parameters are set to get high quality surface finish and part properties.
- We use an EOS M280 Direct Metal Laser Sintering machine with a build envelope of 250mm x 250mm x 300mm equipped with a 400W Laser.
- To prevent oxidation, the build chamber is filled with inert gas and the oxygen content in the chamber is maintained at less than 0.1%.
- The parts are built on a pre-heated metal substrate which keeps going down by a layer thickness after each layer is printed, until the final layer is printed.
- Once printing is done, the part is allowed to cool down for a short period and the parts are unloaded for further post-processing.
Post Processing
Post Processing
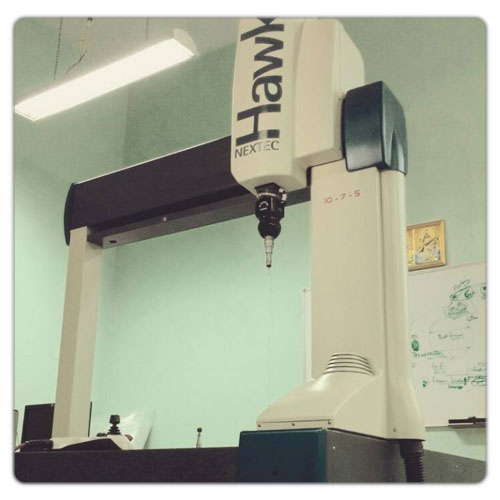
- Depowdering: To ensure all the powder is removed from the printed part.
- Heat Treatment: For stress relieving and improving mechanical properties.
- Wire EDM: To cut-off part from the build plate.
- CNC Machining: For support removal and maintaining high tolerance dimensions.
- Surface Finishing: To get the desired finish on the part.
- Dimensional Inspection: To verify if the dimensions are as per the model and drawing.
- Structural Inspection: To verify if there are any cracks or internal defects in the part.
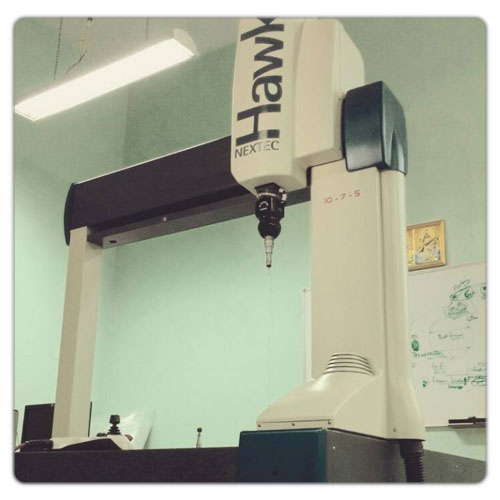
- Depowdering: To ensure all the powder is removed from the printed part.
- Heat Treatment: For stress relieving and improving mechanical properties.
- Wire EDM: To cut-off part from the build plate.
- CNC Machining: For support removal and maintaining high tolerance dimensions.
- Surface Finishing: To get the desired finish on the part.
- Dimensional Inspection: To verify if the dimensions are as per the model and drawing.
- Structural Inspection: To verify if there are any cracks or internal defects in the part.
Benefits of Metal 3D Printing
Benefits of Metal 3D Printing
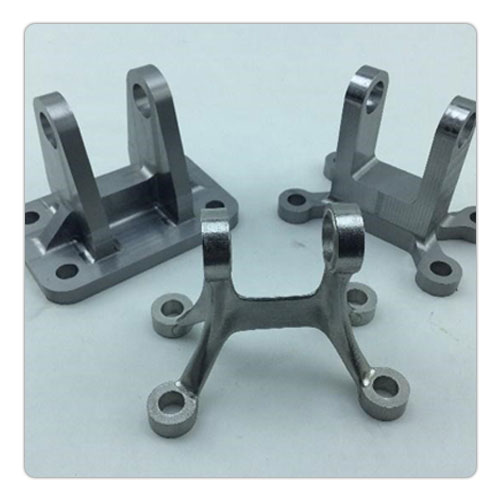
Weight Reduction
Topology optimised part with 35% reduced weight compared to a traditional design.
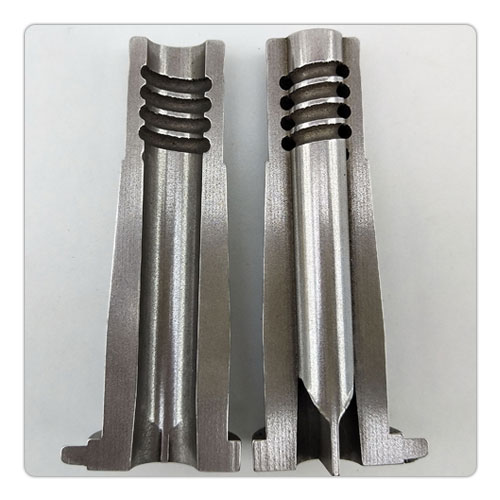
Improved Functional Performance
Tooling insert with conformal cooling used in Injection Moulding for faster cycle time.
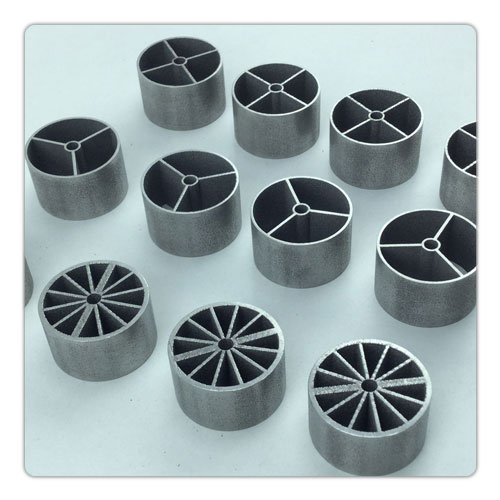
Mass Customization
Parts with minute design changes printed in a single build to validate the design.
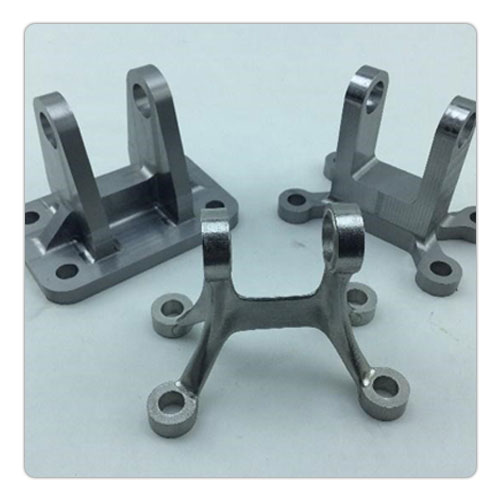
Weight Reduction
Topology optimised part with 35% reduced weight compared to a traditional design.
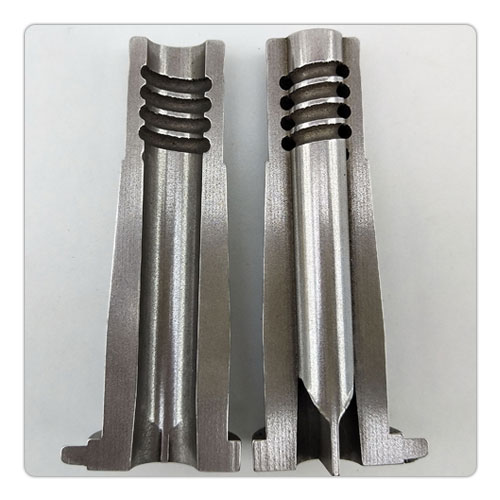
Improved Functional Performance
Tooling insert with conformal cooling used in Injection Moulding for faster cycle time.
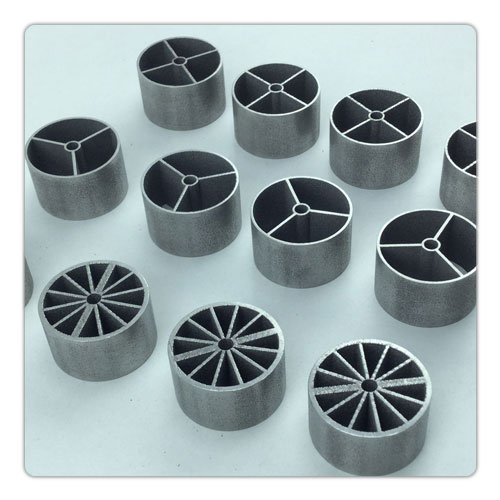
Mass Customization
Parts with minute design changes printed in a single build to validate the design.
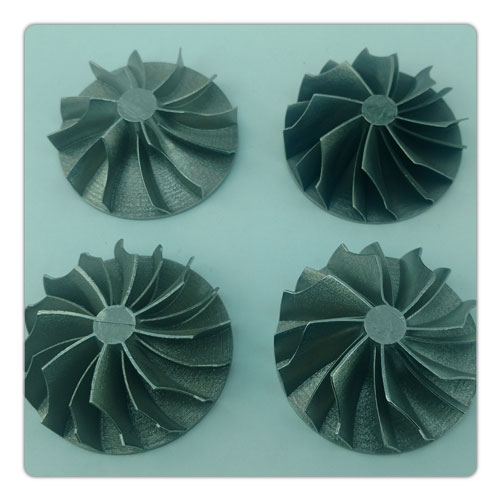
Quick Batch Production
Multiple parts printed in one shot for faster lead times and tool less production.
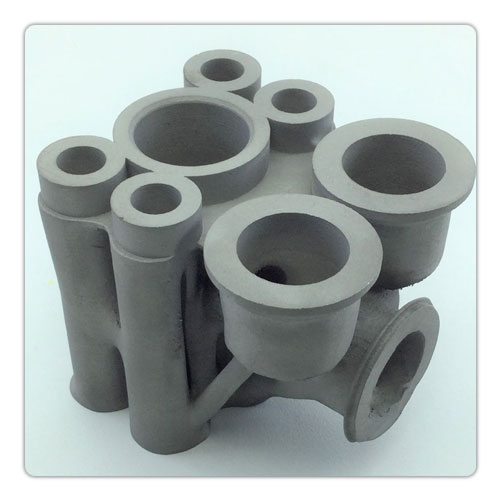
Improved Freedom of Design
A manifold designed for lesser fluid resistance which increases the working efficiency.
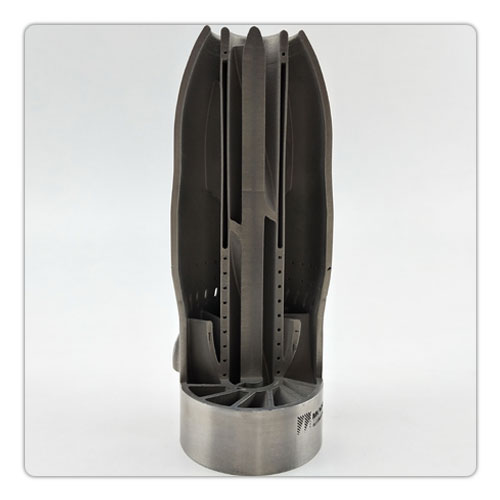
Part Consolidation
A highly complex design of Fuel Injector and Swirler redesigned and built as a single piece.
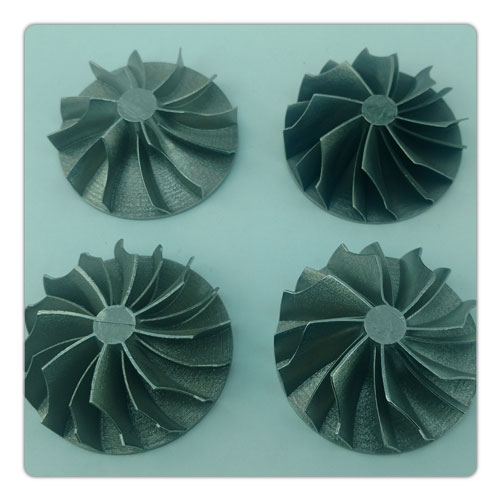
Quick Batch Production
Multiple parts printed in one shot for faster lead times and tool less production.
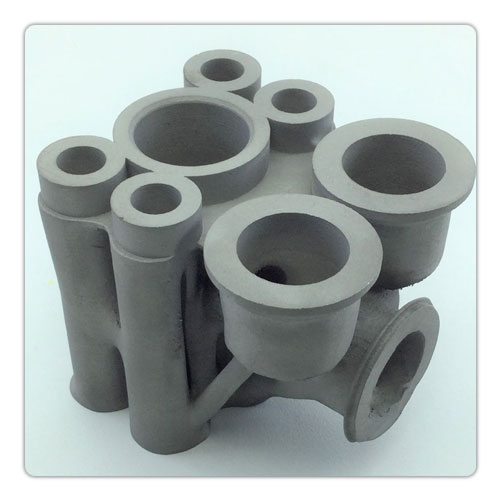
Improved Freedom of Design
A manifold designed for lesser fluid resistance which increases the working efficiency.
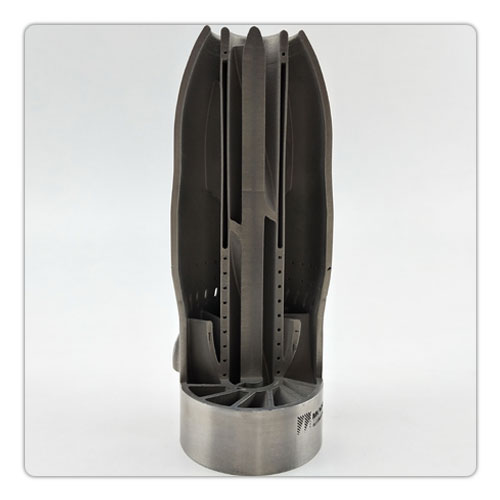
Part Consolidation
A highly complex design of Fuel Injector and Swirler redesigned and built as a single piece.
Common Material Grades Available in DMLS
Common Material Grades Available in DMLS
Stainless Steel
- Corrosion Resistant
- Ductile
- Good Machinability
Wide range of applications in food industry, surgical tools, watches and jewellery.
Aluminium Alloys
- Good Thermal Prop
- Strength & Hardness
- Good Machinability
Wide range of applications in prototype parts, automotive and aircraft interiors.
Nickel Alloys
- Heat Resistant
- Corrosion Resistant
- Performs Even at 700° C
Wide range of applications in aircraft, space and turbine components.
Tool Steels
- Good Thermal Conductivity
- Easily Machinable
- Hardenable Upto 55 HRC
Wide range of applications in tooling and series production parts.
Titanium Alloys
- Light Weight with Strength
- Bioadhesion
- Corrosion Resistant
Wide range of applications in biomedical, aerospace and motor sport industries.
Stainless Steel
- Corrosion Resistant
- Ductile
- Good Machinability
Wide range of applications in food industry, surgical tools, watches and jewellery.
Aluminium Alloys
- Good Thermal Prop
- Strength & Hardness
- Good Machinability
Wide range of applications in prototype parts, automotive and aircraft interiors.
Nickel Alloys
- Heat Resistant
- Corrosion Resistant
- Performs Even at 700° C
Wide range of applications in aircraft, space and turbine components.
Tool Steels
- Good Thermal Conductivity
- Easily Machinable
- Hardenable Upto 55 HRC
Wide range of applications in tooling and series production parts.
Titanium Alloys
- Light Weight with Strength
- Bioadhesion
- Corrosion Resistant
Wide range of applications in biomedical, aerospace and motor sport industries.
Industries & Usage
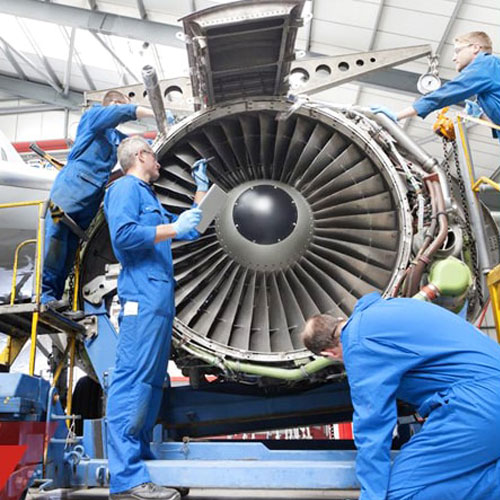
Aerospace
Parts ranging from cabin interiors to complex engine components are now manufactured using Metal 3D Printing. By providing lightweight structures with improved functional performance, AM contributes to the technical improvement of the aerospace industry by reducing material costs, fuel costs and CO2 emissions.
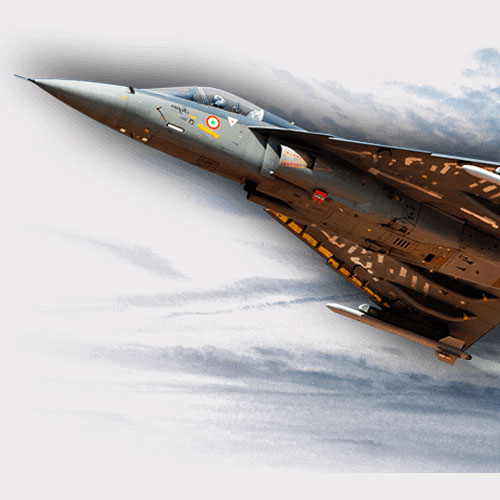
Defence
The strength of a nation is often measured by its defence capability. By using DfaM with Metal 3D Printing, innovative products can be manufactured. By adopting topology optimisation during design stage and then manufacturing through metal 3d printing, the weight of devices carried by soldiers on their back can be reduced.
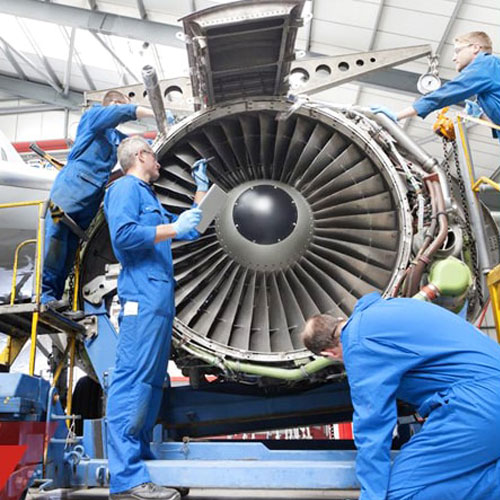
Aerospace
Parts ranging from cabin interiors to complex engine components are now manufactured using Metal 3D Printing. By providing lightweight structures with improved functional performance, AM contributes to the technical improvement of the aerospace industry by reducing material costs, fuel costs and CO2 emissions.
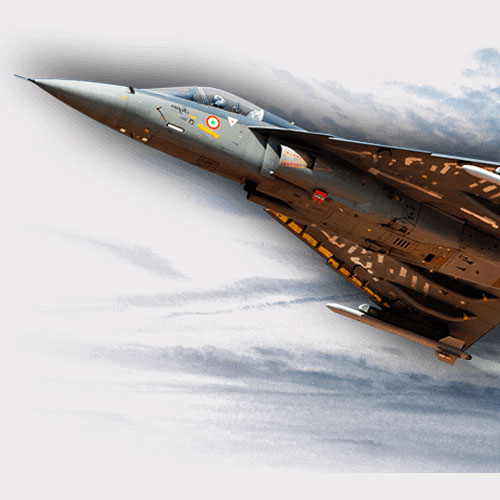
Defence
The strength of a nation is often measured by its defence capability. By using DfaM with Metal 3D Printing, innovative products can be manufactured. By adopting topology optimisation during design stage and then manufacturing through metal 3d printing, the weight of devices carried by soldiers on their back can be reduced.
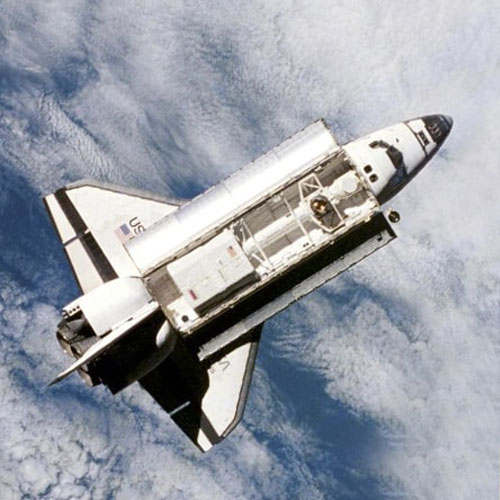
Space
The heavier the weight of launch vehicle, more fuel is required and therefore, more cost. With the help of metal 3D printing, weight of the launch vehicle can be decreased drastically. High performance alloys like Inconel which are difficult to machine and find application in rocket engines, are processed much easily through 3d printing.
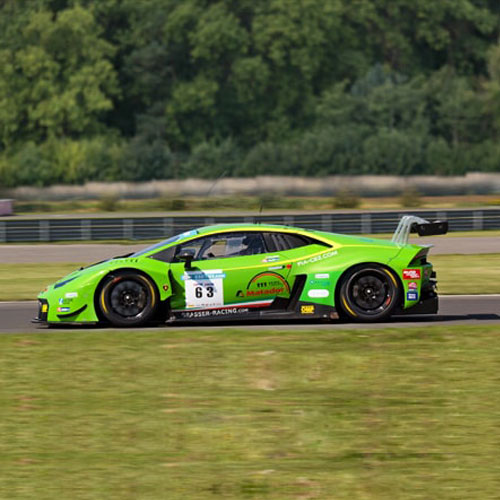
Automotive
Although the Auto industry needs parts in high quantities, AM has applications for Automotive. When developing a new product, all the design variants can be printed and the best among them can be chosen. With the entry of electric vehicles, ergonomic and lightweight parts can be manufactured which increases the efficiency of the vehicle.
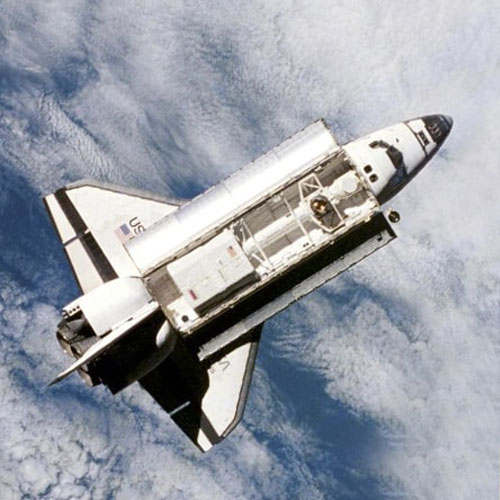
Space
The heavier the weight of launch vehicle, more fuel is required and therefore, more cost. With the help of metal 3D printing, weight of the launch vehicle can be decreased drastically. High performance alloys like Inconel which are difficult to machine and find application in rocket engines, are processed much easily through 3d printing.
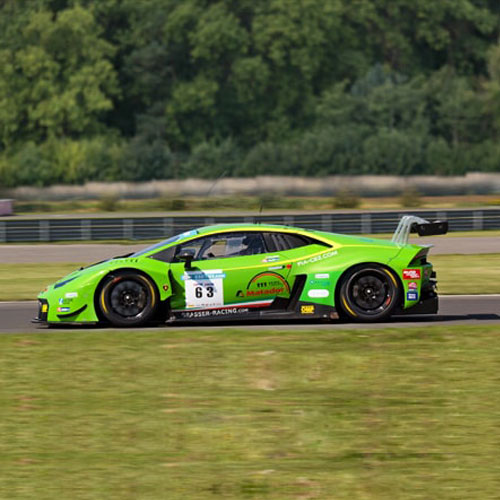
Automotive
Although the Auto industry needs parts in high quantities, AM has applications for Automotive. When developing a new product, all the design variants can be printed and the best among them can be chosen. With the entry of electric vehicles, ergonomic and lightweight parts can be manufactured which increases the efficiency of the vehicle.
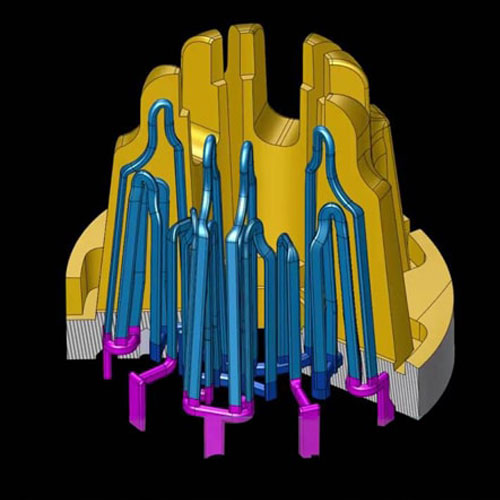
Tooling
Unlike straight cooling channels achieved by drilling, AM produces optimized cooling channels that closely conform to the surface of the mold cavity. This enables for faster heat transfer between the injected material and cooling fluid, resulting in rapid uniform cooling of the injected part, thereby reducing the cycle time and producing better quality parts.
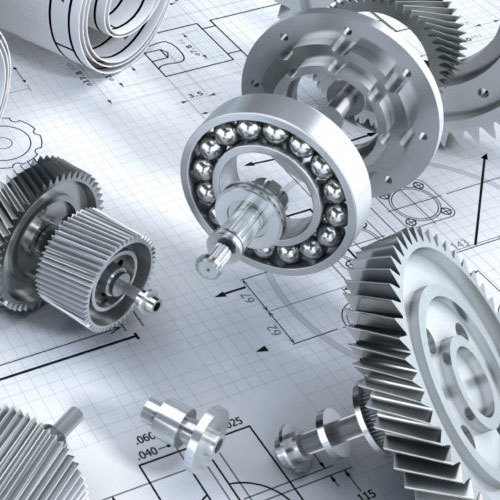
General Engineering
Most of the engineering components can be made feasible for Metal 3D printing. Custom jigs and fixtures can be additively manufactured in a very short lead time. General engineering applications includes prototype parts, small batch production parts as well as custom made parts used to improve an existing process.
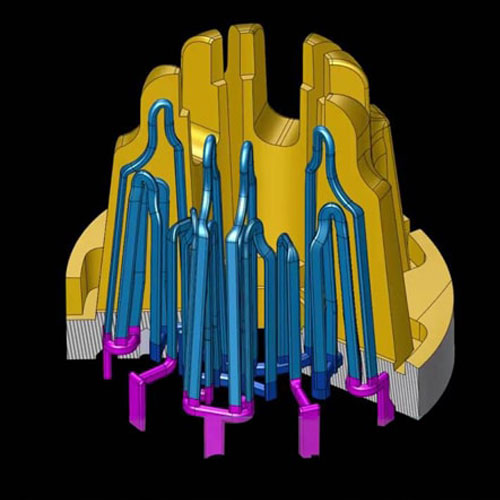
Tooling
Unlike straight cooling channels achieved by drilling, AM produces optimized cooling channels that closely conform to the surface of the mold cavity. This enables for faster heat transfer between the injected material and cooling fluid, resulting in rapid uniform cooling of the injected part, thereby reducing the cycle time and producing better quality parts.
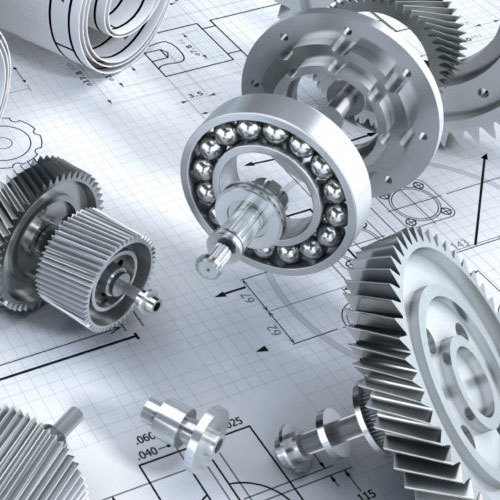
General Engineering
Most of the engineering components can be made feasible for Metal 3D printing. Custom jigs and fixtures can be additively manufactured in a very short lead time. General engineering applications includes prototype parts, small batch production parts as well as custom made parts used to improve an existing process.
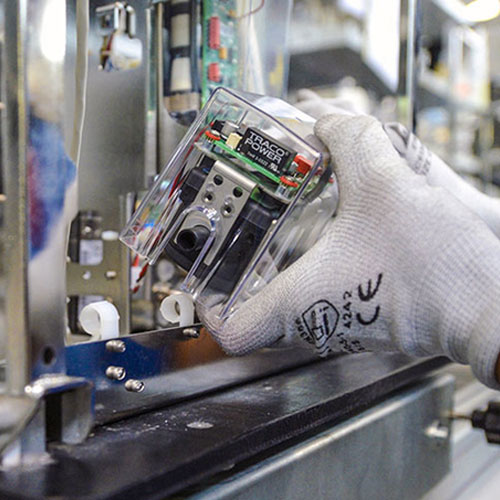
Medical
Surgical tools made in stainless steel are now manufactured using 3d printing. A proto sample is made through metal AM and then tested for its performance. In trauma cases where implants are needed due to bone damage, metal printing produces custom implant specific to each patient which reduces the possibility of a re-surgery.
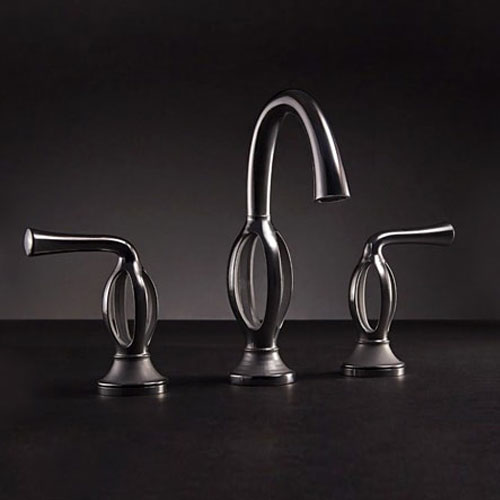
Art
With the way we are evolving, everything will be customised for everybody. Additive manufacturing for artistic items unveils huge potential due to freedom for complex design and customization it can offer. Comprising from customised watches, jewellery to ancient art, the art and fashion world can use 3d printing for their every need.
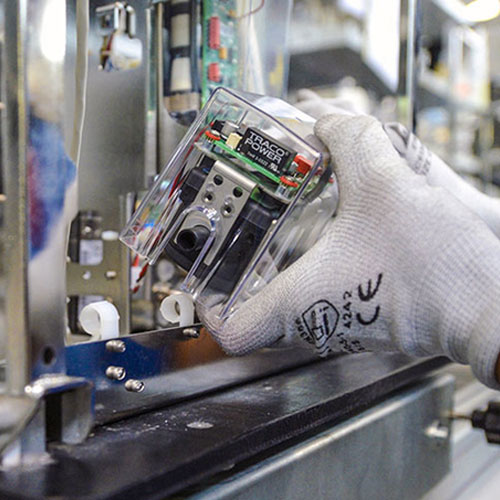
Medical
Surgical tools made in stainless steel are now manufactured using 3d printing. A proto sample is made through metal AM and then tested for its performance. In trauma cases where implants are needed due to bone damage, metal printing produces custom implant specific to each patient which reduces the possibility of a re-surgery.
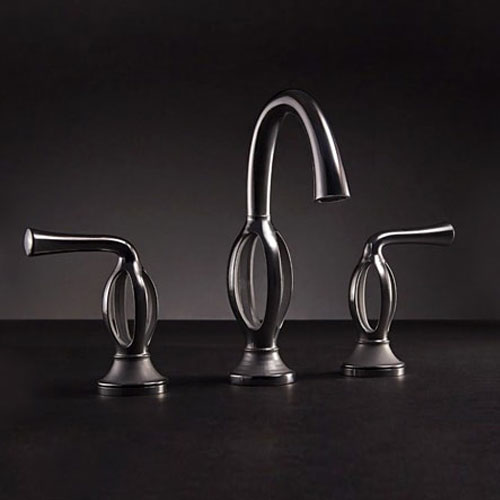
Art
With the way we are evolving, everything will be customised for everybody. Additive manufacturing for artistic items unveils huge potential due to freedom for complex design and customization it can offer. Comprising from customised watches, jewellery to ancient art, the art and fashion world can use 3d printing for their every need.
Research & Development
Research & Development
New Material Development
Out of the plethora of metal alloys available in bar stock form, only around 8 to 10 metal grades are currently available for DMLS. Based on your specification, we can get powders of a certain alloy made through Gas Atomisation. This powder then undergoes extensive research at our facility.
Parameter Optimization
Based on your application and requirement, we optimize the process parameters for desired part properties. Requirements could be a better surface finish, higher productivity or a mixture of both. Our R&D activity includes experimenting these parameters and testing it for the desired output.
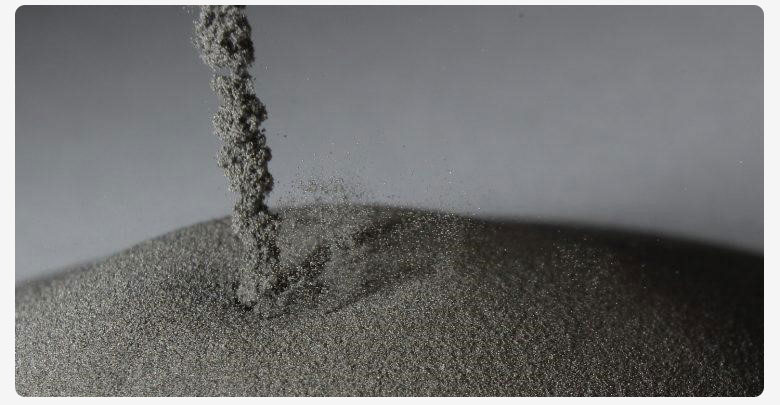
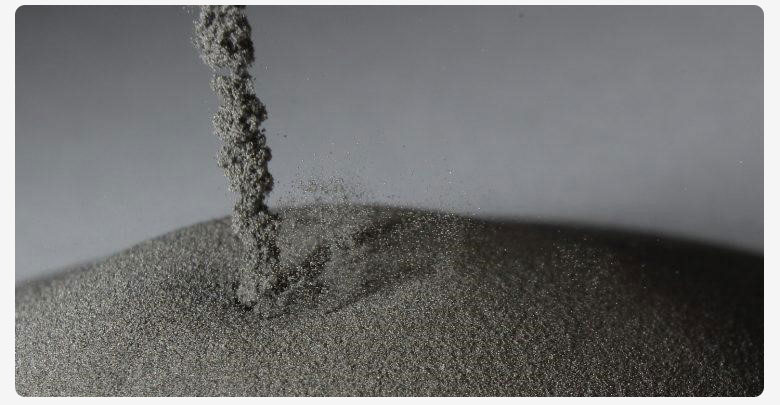
New Material Development
Out of the plethora of metal alloys available in bar stock form, only around 8 to 10 metal grades are currently available for DMLS. Based on your specification, we can get powders of a certain alloy made through Gas Atomisation. This powder then undergoes extensive research at our facility.
Parameter Optimization
Based on your application and requirement, we optimize the process parameters for desired part properties. Requirements could be a better surface finish, higher productivity or a mixture of both. Our R&D activity includes experimenting these parameters and testing it for the desired output.
General FAQs
General FAQs
Direct Metal Laser Sintering (DMLS), Selective laser Melting(SLM) and Direct Metal Printing(DMP) are all the same. It is basically Powder Bed Melting process using a laser source. Different Machine Manufacturers use different names to promote their brand.
Our machine has a build volume of 250mm x 250mm x 300mm in the x,y and z directions respectively. So, any component within that envelope can be built. However, bigger parts can be cut into sections and these printed sections can be joined through welding to get the final product.
Since it is a Powder Bed process, it is currently impossible to print 2 different alloys simultaneously. However, we can print with a certain alloy up to some height, and then continue printing with a different alloy from that height.
The virgin powder after its first use goes through a sieving process to separate condensate material from the good powder. The condensate is scrapped and the sieved powder is used for the next build. A ball –park value for material wastage can be taken as 5% of the part weight.
Direct Metal Laser Sintering (DMLS), Selective laser Melting(SLM) and Direct Metal Printing(DMP) are all the same. It is basically Powder Bed Melting process using a laser source. Different Machine Manufacturers use different names to promote their brand.
Our machine has a build volume of 250mm x 250mm x 300mm in the x,y and z directions respectively. So, any component within that envelope can be built. However, bigger parts can be cut into sections and these printed sections can be joined through welding to get the final product.
Since it is a Powder Bed process, it is currently impossible to print 2 different alloys simultaneously. However, we can print with a certain alloy up to some height, and then continue printing with a different alloy from that height.
The virgin powder after its first use goes through a sieving process to separate condensate material from the good powder. The condensate is scrapped and the sieved powder is used for the next build. A ball –park value for material wastage can be taken as 5% of the part weight.
Speak to Our Additive Manufacturing Experts
Our experts are here to help you create complex mechanical components using DMLS technology. Book a free call below with our experts to find out how you can make the best use of Metal 3D Printing.
Speak to Our Additive Manufacturing Experts
Our experts are here to help you create complex mechanical components using DMLS technology. Book a free call below with our experts to find out how you can make the best use of Metal 3D Printing.